- رزومه شرکت
- فرم های درخواست
- فرم درخواست ارماتور یاب
- فرم درخواست چشک اشمیت
- فرم درخواست آزمایش بتن
- فرم درخواست آزمایش برق
- فرم درخواست آزمایش پلی استایرن
- فرم درخواست آزمایشات مصالح مسیر راه
- فرم درخواست آزمایش بارگذاری سقف
- فرم درخواست آزمایش آسفالت
- فرم درخواست آزمایش جوش
- فرم درخواست آزمایش ژئوتکنیک
- فرم درخواست آزمایش طرح اختلاط
- فرم درخواست آزمایش کرگیری
- فرم درخواست آزمایش کشش میلگرد
چرا بازرسی جوش ؟
جوشکاری یکی از مهمترین فرآیندهای اتصال در صنایع مختلف از جمله ساختمانسازی، صنایع نفت و گاز، پتروشیمی، خودروسازی و صنایع دریایی است. کیفیت جوش تأثیر مستقیم بر استحکام، دوام و ایمنی سازهها دارد. ازاینرو، بازرسی جوش یک ضرورت غیرقابلانکار است که به تضمین کیفیت، جلوگیری از خرابیهای احتمالی و افزایش ایمنی کمک میکند. در این مقاله به دلایل اهمیت بازرسی جوش، انواع روشهای آن و استانداردهای مربوطه پرداخته خواهد شد.
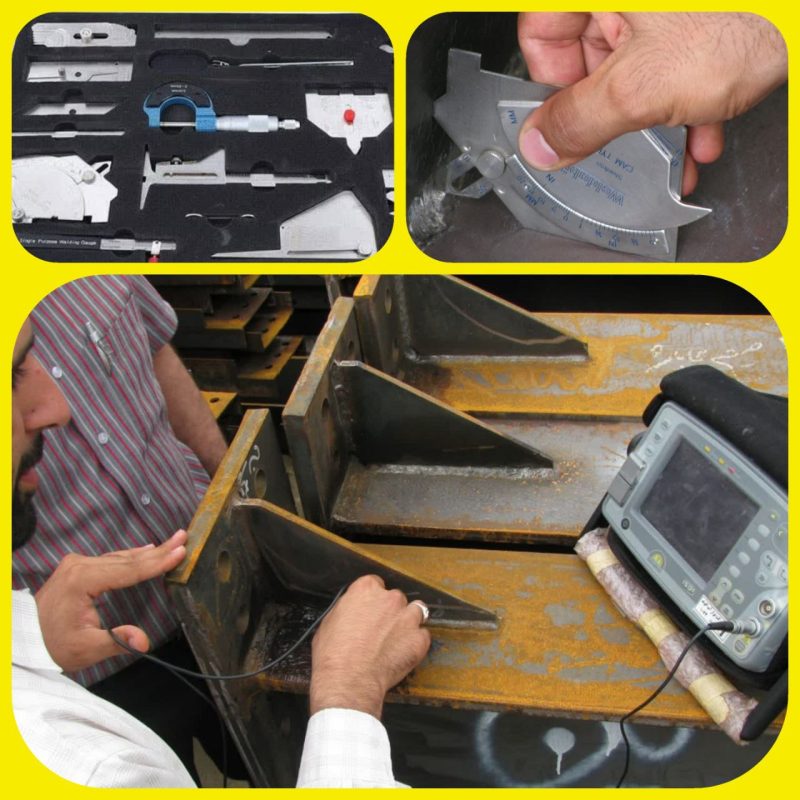
1. اهمیت بازرسی جوش
بازرسی جوش با اهداف متعددی انجام میشود که برخی از مهمترین آنها عبارتند از:
1.1. افزایش ایمنی سازهها
اتصالات جوشکاری شده، بهویژه در پروژههای حساس مانند پلها، مخازن تحت فشار، سکوهای نفتی و سازههای دریایی، باید مقاومت کافی در برابر بارهای مکانیکی و محیطی داشته باشند. وجود ترکها، تخلخلها و عیوب دیگر در جوش میتواند منجر به شکست فاجعهبار سازه شود.
1.2. جلوگیری از هزینههای سنگین تعمیر و نگهداری
یک جوش معیوب ممکن است در مراحل اولیه بهرهبرداری مشکلی ایجاد نکند، اما با گذر زمان و تحت تأثیر تنشهای مکانیکی، حرارتی یا محیطی، آسیبهای شدیدی به سازه وارد کند. هزینههای تعمیر و تعویض یک جوش نامناسب بسیار بیشتر از هزینههای بازرسی اولیه آن است.
1.3. افزایش طول عمر سازهها
جوشهای با کیفیت، استحکام سازه را تضمین کرده و باعث افزایش طول عمر مفید آن میشوند. بهویژه در صنایع نفت و گاز و پتروشیمی که تأسیسات در معرض خوردگی، دماهای بالا و فشارهای زیاد قرار دارند، اطمینان از کیفیت جوش ضروری است.
1.4. رعایت استانداردهای ملی و بینالمللی
در پروژههای صنعتی، رعایت استانداردهای جوشکاری الزامی است. بسیاری از کدها و استانداردهای بینالمللی مانند AWS D1.1، ASME Section IX، API 1104 و ISO 9606، نیازمند انجام بازرسی جوش در مراحل مختلف هستند.
2. انواع روشهای بازرسی جوش
بازرسی جوش به دو دسته اصلی بازرسی چشمی (VT) و بازرسیهای غیرمخرب (NDT) تقسیم میشود. هرکدام از این روشها مزایا و محدودیتهای خود را دارند.
2.1. بازرسی چشمی (Visual Testing – VT)
بازرسی چشمی، سادهترین و متداولترین روش بازرسی جوش است که توسط بازرس مجرب انجام میشود. این روش شامل بررسی سطحی برای یافتن ترکها، تخلخلها، بریدگیهای کناری و دیگر ناپیوستگیهای سطحی است. بازرسی چشمی معمولاً بهعنوان اولین گام در فرآیند کنترل کیفیت جوش محسوب میشود.
2.2. بازرسی با مایعات نافذ (Liquid Penetrant Testing – PT)
در این روش، مایع نافذی که دارای قابلیت نفوذ بالا است، روی سطح جوش اعمال شده و پس از مدت مشخصی پاک میشود. سپس از یک آشکارساز (Developer) برای مشخص کردن ناپیوستگیهای سطحی مانند ترکها و منافذ ریز استفاده میشود.
2.3. بازرسی با ذرات مغناطیسی (Magnetic Particle Testing – MT)
این روش برای مواد فرومغناطیسی مناسب است. در این روش، میدان مغناطیسی در قطعه ایجاد شده و در صورت وجود ترک یا عیب، ذرات مغناطیسی در نواحی نقص تجمع پیدا میکنند که بازرسان میتوانند آنها را مشاهده و تحلیل کنند.
2.4. بازرسی التراسونیک (Ultrasonic Testing – UT)
در روش تست التراسونیک، امواج فراصوتی به داخل جوش ارسال میشوند و بازگشت آنها مورد تجزیهوتحلیل قرار میگیرد. این روش قادر است عیوب داخلی جوش مانند ترکها، نفوذ ناقص و ناپیوستگیهای داخلی را شناسایی کند.
2.5. بازرسی با پرتوهای رادیویی (Radiographic Testing – RT)
در این روش از پرتوهای X یا گاما برای بررسی عیوب داخلی جوش استفاده میشود. فیلم یا سنسور دیجیتالی که در طرف دیگر قطعه قرار دارد، میزان جذب اشعه را ثبت کرده و تصویر حاصل، نقصهای موجود در جوش را نشان میدهد. این روش یکی از دقیقترین روشهای بازرسی جوش محسوب میشود.
2.6. تست جریان گردابی (Eddy Current Testing – ET)
این روش بر پایه القای الکترومغناطیسی عمل کرده و برای تشخیص ترکهای سطحی و زیرسطحی در فلزات رسانا کاربرد دارد.
3. استانداردهای مرتبط با بازرسی جوش
استانداردهای بینالمللی متعددی برای کنترل کیفیت جوش تدوین شدهاند که مهمترین آنها عبارتند از:
- AWS D1.1: استاندارد جوشکاری سازههای فولادی
- ASME Section IX: استاندارد جوشکاری برای دیگهای بخار و مخازن تحت فشار
- API 1104: استاندارد جوشکاری خطوط لوله انتقال نفت و گاز
- ISO 9606: استاندارد صلاحیت جوشکاران
- EN 1090: استاندارد جوشکاری سازههای فلزی در اروپا
4. چالشهای بازرسی جوش
4.1. هزینه و زمانبر بودن
برخی از روشهای بازرسی جوش مانند رادیوگرافی و تست التراسونیک هزینهبر و نیازمند تجهیزات تخصصی هستند. بااینحال، هزینههای ناشی از خرابیهای سازهای بسیار بیشتر از هزینههای بازرسی اولیه است.
4.2. تفسیر نتایج بازرسی
برخی از روشهای غیرمخرب مانند UT و RT نیاز به کارشناسان متخصص برای تفسیر نتایج دارند. اشتباه در تفسیر میتواند منجر به عدم شناسایی نقصهای بحرانی یا رد اشتباه جوشهای سالم شود.
4.3. دسترسی محدود به برخی مناطق جوشکاری شده
در برخی سازهها، امکان دسترسی به محل جوشکاری وجود ندارد و این امر اجرای برخی روشهای بازرسی را دشوار میکند.
خدمات ما
5. نتیجهگیری
بازرسی جوش یکی از مهمترین اقدامات در فرآیند کنترل کیفیت در صنایع مختلف است. این فرآیند نهتنها از بروز خرابیهای سازهای جلوگیری میکند، بلکه باعث کاهش هزینههای نگهداری، افزایش طول عمر سازه و ارتقای سطح ایمنی میشود. با توجه به نوع سازه و استانداردهای موردنیاز، انتخاب روش مناسب بازرسی جوش ضروری است. رعایت دقیق این فرآیند میتواند از بروز حوادث ناگوار و خسارات جبرانناپذیر جلوگیری کند.